Shot blasting is a fast and cost effective process for smoothening rough metal surfaces. It is commonly employed to restore old equipment and steelwork, removing dirt, grease, rust and old paint in preparation for repainting. Our shot blasting gallery shows several examples of how we have applied this in practice.
Figure 1: A motor-trike frame before and after shot blasting and repainting.
Surface Preparation
Before applying a coating on a metal surface, whether paint or a protective powder, it must be prepared adequately. Shot blasting achieves this by abrading the surface with a high pressure stream of silicon grit, or shot. A host of industries use shot blasting as part of the finishing processes for steel fabrications, as well as equipment restoration.
Durability is one reason shot blasting has become a preferred surface preparation method – with superior results to chemical cleaning. Equipment and products that are put through abrasive blasting exhibit better paint adhesion and a longer service life. Why is this?
Longer Lasting Surfaces Bonds
Shot blasting is highly effective in eliminating impurities on surfaces. It removes all forms of debris and corrosive builds such as faded paint, rust and chemical stains. The smooth surface that results from thorough preparation makes it easy for a protective coating or paint to bond. Whether a product will be galvanised, enamelled or electroplated, the coating sticks without difficulties. A permanent bond ensures that equipment is always protected from contaminants, allowing it to last longer.
Figure 2: An old fashioned box radiator before shot blasting...
Figure 3: After - with the addition of a protective coat of top paint.
No Chemical Use
The eco-friendliness of the process contributes to the durability of surfaces. Chemical deposits such as those left over from paint stripping fluids can eat away at metal and lead to premature degradation of equipment. An environmentally safe surface has the potential to last longer because it doesn't demand a lot of maintenance to retain its condition. The shot blasting process doesn't necessitate the removal of a layer of metal from the surface as with other processes, so it doesn’t weaken the metal.
Detect Surface Defects
The lifespan of your equipment can shorten significantly if faults go unnoticed for an extended period. Shot blasting provides an opportunity for technicians to identify defects on the surface before it goes through finishing. Early detection gives you a chance to repair the surface, which goes a long way in improving its durability.
Remove Rust
Rust is the biggest threat to metal surfaces that contain iron. This type of corrosion causes a flaky powder to form on the metal surface, replacing the steel. Rust is so common that we are all used to seeing it on metal surfaces, but it is by no means harmless. Continued build-up of rust will weaken the surface, making it susceptible to the smallest structural threats. Furthermore, rust will continue to damage a surface even if it is painted over with a top coat. Rust has to be removed before repainting. Abrasive blasting effectively eliminates rust from surfaces so that it doesn't affect the protective coating.
Figure 4: Closeup of a section of steel framework showing advanced rust build-up - plus old paint residues and bird droppings (corrosive due to their acidity)
Figure 5: The same steel work looking as good as new; following shot blasting and repainting.
Metal surfaces require the highest standards of care if they are to survive exposure to atmospheric contaminants. The surface preparation and type of finish are two elements that influence the durability of metal products. Shot blasting is a cost-effective option for cleaning all types of metal surfaces. The process is suitable for large and small projects, whether it's restoring, building or protecting metal products.
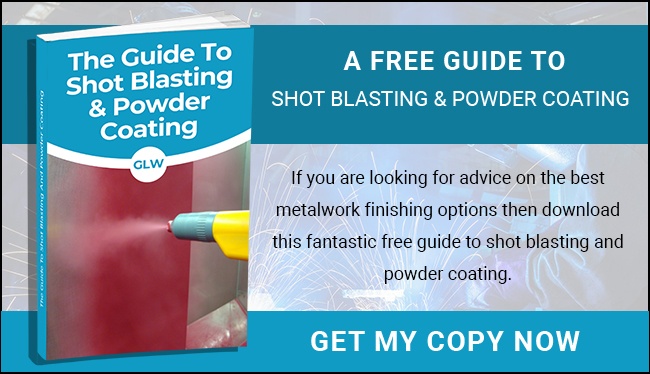