Introduction
Protecting metalwork as thoroughly as possible against corrosion and abrasion is critical to maintaining its structural integrity and promoting longevity. Equally important is thorough surface preparation of the workpiece before applying any protective coating.
Powder coating is the most popular protective treatment for a whole range of metal items from handrails to garden furniture. Prior to applying the powder coating, we subject the item to shot blasting to remove all traces of previous paint or coating, rust and dirt.
GLW Engineering made a strategic decision to keep these and other metal treatment processes in-house to maintain the required high level of quality control.
What Is Shot Blasting?
Shot blasting is the process of abrading the surface of a metal workpiece to remove rust, dirt and other solidified contaminants by hurling a high speed stream of tiny pieces of stainless steel that resemble buckshot. It is capable of deburring, shaping and texturing a surface.
What's The Difference Between Shot Blasting & Sandblasting?
Sandblasting uses compressed air to direct a jet of sand at an object to abrade it. It is highly effective but creates a great deal of silicon dust.
In shot blasting, the metal shot is poured into a turbine. The blades, rotating at high speed, project the shot against the surface of the metal workpiece with great force. As rust and dirt is removed, it is sucked out of the stream of spent shot, which is then recycled to be used again.
- Sandblasting can be carried out with a hand held gun, while shot blasting requires an enclosed space through which the workpiece is passed.
- Shot blasting delivers a much more powerful impact on the surface of the workpiece than sandblasting. This effect can generate textured surfaces and shaping that cannot be achieved with sandblasting.
Our Facilities
Some years ago our team invested in a high quality shot blasting system. Using its specialist settings, customers may request a texture for certain finishes.
Shot blasting is not guaranteed to remove soft contaminants like oil, grease and silicone, which can result in patches on the powder coated surface. To ensure that all invisible contaminants are removed, pre-treatment can include soda blasting, which means no chemicals are required.
Click here to view our YouTube video.
What Is Powder Coating?
Special finely ground polymers (resin) are mixed with pigments to create a thermosetting epoxy powder of particles from 5 to 110 µ that is sprayed onto an electro-statically charged workpiece so that the powder adheres. It is then cured for about 15 minutes at approximately 200°C which causes the polymers to melt, flow and fuse to create a skin that is generally tougher and harder wearing than paint. Layer thickness can be from 20 to 300 µ.
The result is a homogenous aesthetic surface that is a durable and long lasting protective coating with a pleasing texture and colour. It offers high gloss retention with excellent resistance to UV, corrosion, chemicals, abrasion and heat. Powder coating can be used on practically every type of metal as well as some other substrates such as plastics.
The polymers may be thermoset or thermoplastic. Thermoplastic polymers are less rigid than thermoset and ideal for items that may experience movement, such as garden benches. Thermoset polymers are more suited to fixed applications such as architectural fabrications on buildings.
The process was developed in the US during the 1960s. Nowadays, there is a wide variety of powder chemistry to suit specific applications.
We can powder coat aluminium, mild steel, galvanised steel and stainless steel as standard, but our service is not limited to those. We are always happy to innovate to meet specific requirements.
Why Is Powder Coating Better Than Paint?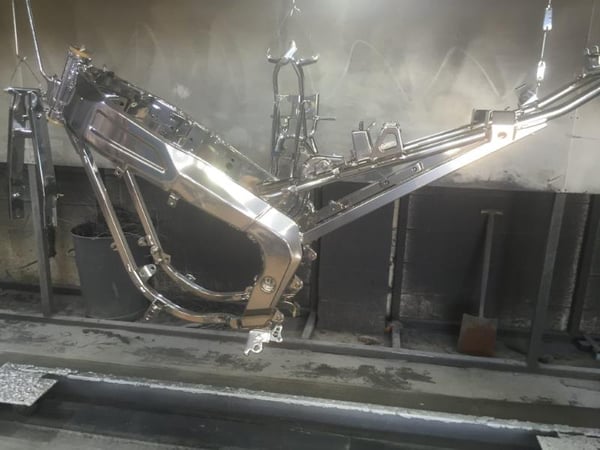
Liquids like paint have a recognised set of drawbacks, such as drips, sags and long drying time. Paint is also classified as hazardous waste which requires specialist disposal. An undercoat and topcoat are often required with a drying interval in-between, which doubles the work and labour cost. Also, contaminants can enter the liquid paint while it is drying.
Powder coating is environmentally friendly, contains no solvents and generates no carcinogens or other hazardous by-products. Up to 90% excess unused powder is recovered for reuse. It dries in 15 minutes during curing - then it is ready to go. It is also usually harder wearing than paint.
The Powder Coating Process Explained
There is a 3-step process involved:
- Pre-treatment of the workpiece to clean it and prepare the surface
- Spraying on the powder coating
- Curing
Pre-treatment is a critical requirement for top quality powder coating. Preparation of metal workpieces can involve shot blasting or sand blasting in combination with a process to remove oils and grease. The extent of the treatment really depends on the end use of the object.
For example, a vehicle wheel that will be subject to hostile environments is deserving of more intensive anti-corrosion metal treatment, such as zinc galvanising, before being powder coated. An indoor object may just need to be properly cleaned and washed in a detergent solution in preparation for powder coating.
Spraying requires that the object is properly electro-statically earthed, with the spray gun providing the charged particles. It is carried out in spray booths to restrict the environment in which the powder is sprayed.
Curing can be done in any non-gas oven but commercial curing ovens use electrical or infra-red heat sources. It takes between 15 to 20 minutes at a temperature of approximately 200°C.
Maintaining Powder Coated Surfaces
Like any exposed surface, both outdoor and indoor powder coated items may attract dirt and grime. Handrails, for example, receive constant applications of oil and grease from contact with hands while many external fittings are subject to pollution and substances in the air, which varies with different environments.
Regular Cleaning
Maintaining a regular building maintenance schedule is the best way to preserve your powder coated surfaces. For large buildings, a professional cleaning firm or specialist contractor is recommended that recognises the specific cleaning requirements and will provide written confirmation of cleaning activities for your records.
Cleaning is simple with the primary considerations being:
- Avoid using abrasive tools or substances
- Use only mild detergents from a recommended list (such as Flash in water)
- Scrub with soft cloth or natural bristle brushes
Frequency depends on the external environment:
- Common or normal urban environments should be cleaned every 12 months
- Marine, high pollution (such as motorways), industrial environments and swimming pools should be cleaned every 3 months
Touching Up Minor Damage
Accidents will happen and the powder coating skin may be damaged to the extent that the substrate is exposed. This runs the risk of water ingress and corrosion, and therefore needs to be attended to.
For small areas, it is recommended to use specialist aerosol spray paint for remedial work. Simply contact GLW Engineering & Construction for further detailed advice, or to carry out the work if required.
Why Choose GLW Engineering & Construction?
Since 1992 we have been growing our steel fabrication business steadily through a reputation for delivering high quality results on time. In our line of work we depend a great deal on repeat orders from a number of regular customers. We have been able to achieve that objective only by being consistently reliable and putting a high emphasis on customer satisfaction.
We developed in-house treatments like hot zinc spray galvanising, shot blasting and powder coating. That means no extra costs for you to transport structures to external specialists, and we also get the job done faster. That demonstrates how we approach our work – by thinking like our customers do and taking into account what they want from a steel fabricator.
Our ethos is to strive to understand our customers’ requirements, offer creative advice and support when asked, and complete work to the highest standards and quickly. We use time tested processes and fabrication techniques to guarantee the best result each time.
CE Marking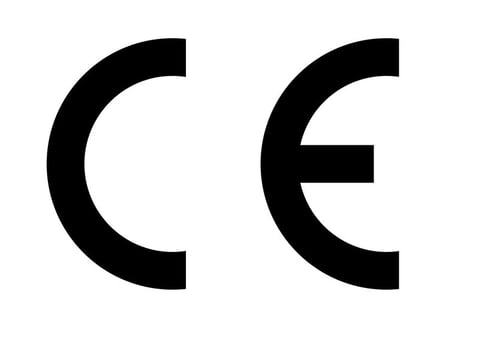
You need to be confident that your steel fabricator implements the full range of applicable quality standards and regulations. That assurance is critical to ensuring that everything you deliver for your client’s project is compliant. The ‘harmonised standards’ for CE marking that we adhere to are the EU technical regulations for steel:
- BS EN 1090-1 for fabricated structural steel
- BS EN 15048-1 & BS EN 14399-1 for structural bolts
- BS EN 10025-1 for steel plates
- BS EN 10210-1 for hot finished hollow sections and BS EN 10219-1 for cold form welded hollow sections
The CPR requires a declaration of performance and CE marking for all structural and weight-bearing steel fabrications. We go further and demonstrate compliance with CE approval for all our fabricated steel components, including railings and balustrades.
Experience & Expertise
We are proud of our wide range of steel fabrication experience and have a portfolio of images and testimonials that support it. All our engineers are design and fabrication experts, highly qualified and with many years of experience in their field. We select our team not only as technical experts, but also for their friendly and professional approach to customer service.
Metal fabrication is our passion and our speciality. Creativity and design support are part and parcel of our operation. You get the benefit for no extra charge. This includes state-of-the-art 3D CAD software that we use in our design department for a much faster and better service. We enjoy keeping abreast of innovations and new developments in technology, and adopting them where it benefits our customers.